Perforating Round Tubing
Perforating holes through one side of a round tube can present several unique problems for metal stampers. The most common are tube deformation, punch point chipping, and slug control.
Tube Deformation and Punch Point Chipping
The first two problems, tube deformation and punch point chipping, are typically caused by tube movement. A nesting die can be used to reduce this movement. The ideal nest should be a radius pocket that is machined a few thousandths of an inch larger than the outside diameter (OD) of the tubing. This will help locate the tube and offer some lateral support.
FIGURE 1: The ideal nest should be a radius pocket that is machined a few thousandths of an inch larger than the OD of the tubing.
The depth of this nest should be slightly more than one-half the OD of the tubing to minimize tool marks and reduce tube deformation.
In addition to proper nesting, it is equally important to lock the tube into position using a "V" groove in a spring stripper. A "V" groove with a 60- to 80-degree included angle will prevent tube rolling and offer additional lateral support. Without this die and stripper support, the tube will be deformed while the hole size will be inconsistent and out-of-round.
Slug Control
The third major concern when perforating tubing is slug control. Slugs that do not break free in manufacturing may interfere with mating parts at assembly or break free and rattle around in the part while in use—neither of which is desirable.
One approach of solving this slug problem is to put shear on the point of the punch. Shear angles and contours play a major part in slug control when perforating a hole without a matrix. They minimize the deformation of the tube by preventing the slug from pulling to one side of the hole as the punch penetrates the tube wall.
Several different shear configurations can be applied, some of which are limited to specific types of tubing materials.
A concave shear that nearly matches the OD of the tube works well for ridged plastics and thick-wall aluminum tubing. It locks the slug into place and cuts it free.
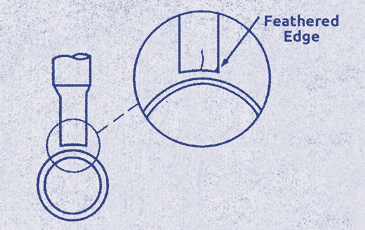
FIGURE 2: This illustrates a concave shear.
Be aware that the two feathered edges are prone to breakage, and wear prematurely. In more severe applications, the feathered edges of a convex shear will chip and the punch may split up the middle.
A flat-bottom punch will work on mild steels. Although not typically considered a shear angle, a flat bottom punch will have a shear effect reducing deformation when perforating contoured material.
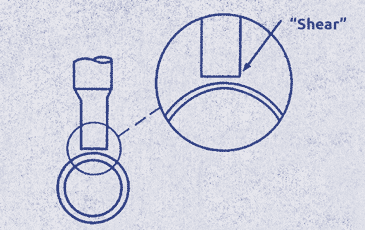
FIGURE 3: This illustrates a flat-bottom punch.
One drawback to a flat-bottom punch is that it does not prevent the slug from pulling to one side. This setup may leave an occasional slug partially attached to the tube.
The most effective shear configuration is a two-dimensional convex radius that is slightly larger than the OD of the tube. It reduces tube deformation while offering good slug control. A positive side effect from this configuration is that it reduces punch-point chipping, making it ideal for stainless steel and thin-wall tubing applications.
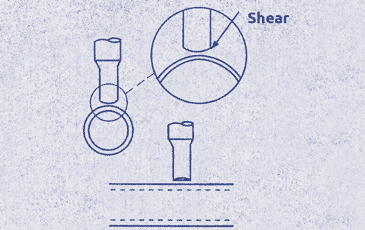
FIGURE 4: Shown here is a convex radius.
Piercing
Another method of slug control is to not remove the slug at all. By piercing instead of perforating, the excess material from the hole is rolled over or formed down into the hole, leaving no free slug to contend with.
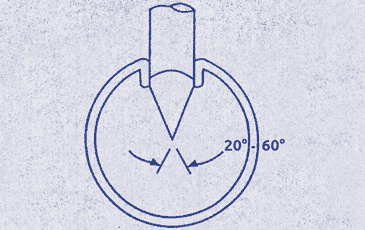
FIGURE 5: Another method of slug control is not to remove the slug at all.
This method of slug control is accomplished by using steep shear angles on the point of the punch. The punch will have three or four flats ground on the point similar to that of a nail. The angle should be between 20 and 60 degrees included.
These shear angles are the result of development (trial and error). Changes in the shear angle will have a direct effect on how much the tube will be flattened or deformed. These angles are limited by how far the tip of the punch can enter through one side of the tube and not contact the opposite wall.
Steeper angles will produce the least amount of deformation, but will be more likely to contact the opposite wall. This type of pierce is most effective when working with aluminum or mild steel.
These are the most common shear configurations. However, many others have been developed and will also work well.
Conclusion
When perforating tubing on a stamping press, please consider the above recommendations. They are sound methods for reducing current problems and will serve as a good foundation for further development.
Perforating tubing through both sides, at an angle, or with a mandrel are considerably different circumstances, all of which are topics in themselves.